This article is adapted from a recent interview with Sparrow’s CEO Meir Veisberg about the importance of user experience in spare parts management. Some parts of the interview have been revised or edited to improve readability in article format.
Sparrow Interview #01: Why user experience matters for spare parts management
Q: I’d like to kick off this interview with a direct question: Why are we talking about user experience? It seems like there are other more important topics related to spare parts, such as the impact of the global supply chain.
First, of course, you’re right, there are many key factors contributing to successful spare parts management. I want to focus on user experience today because I think that (A) it’s something that is typically overlooked, (B) poor user experience has a massive impact on spare parts management, and (C) it’s a topic we can improve on relatively simply (unlike trying to change the global supply chain).
Q: What do you mean by user experience in the context of spare parts management?
User experience means: how satisfied and comfortable people are when they use a product or a process. Now, let's apply this to spare parts management.
Spare parts are managed both physically and digitally. A physical aspect might be how you organize your shelves or where the warehouse is. The digital aspect is similar to a dataset in an Excel file that stores all information regarding the spare parts.
When we combine these two ideas, we see that digital technologies can simplify physical processes.
To answer your question, combining user experience with spare parts management means making it easy and efficient to perform tasks related to spare parts. For example: a common activity is searching for a spare part as part of a maintenance activity. When talking about user experience, we ask the question: How easy is it for the user to perform this search well?
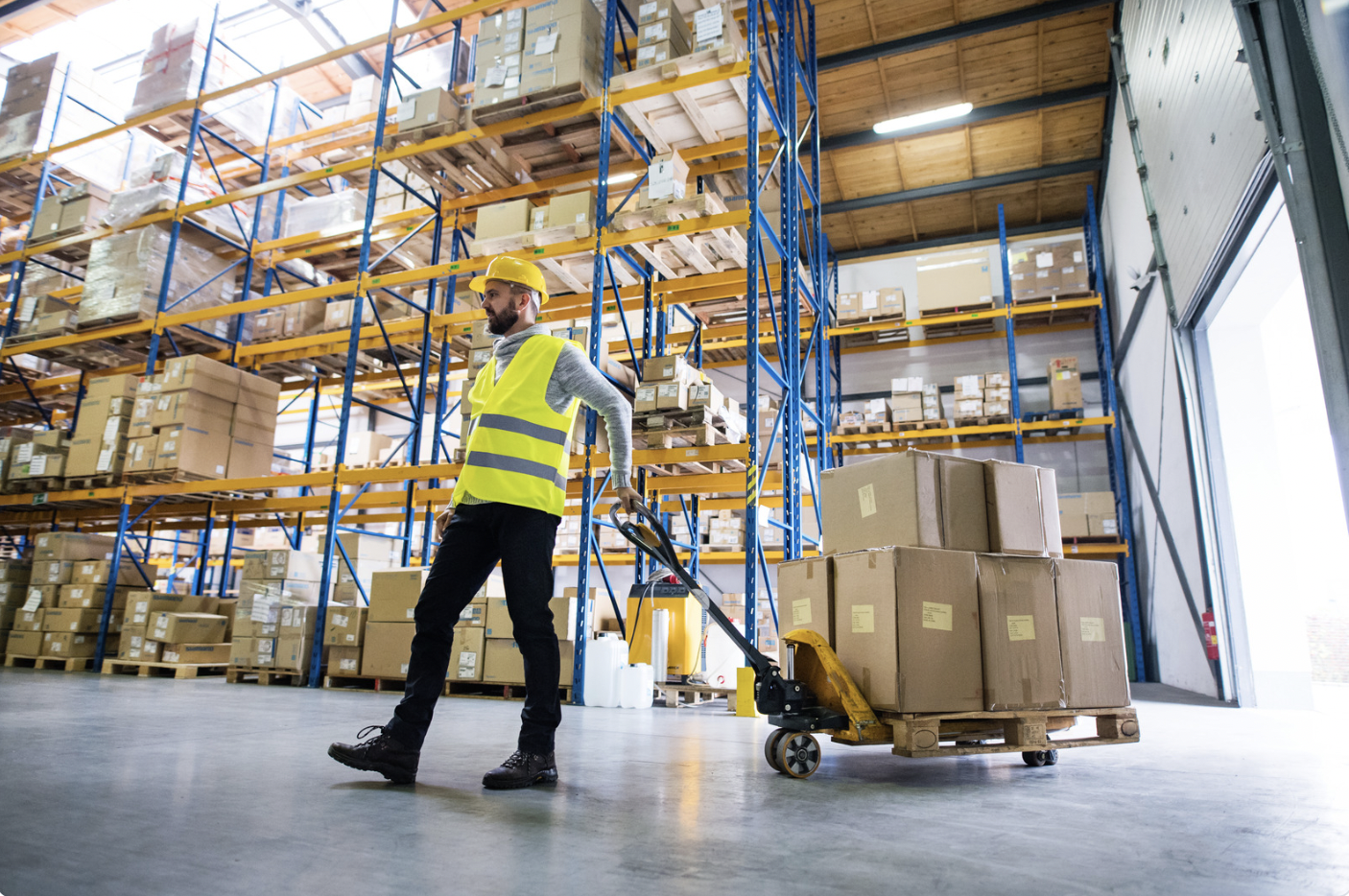
The relationship between spare parts management and good user experience
Q: You mentioned that user experience has a massive impact on spare parts management, what do you mean by this?
When we spoke with spare parts managers or inventory managers, they often showed us tools that were incredibly difficult to understand or use, requiring many steps to complete a job.
They explained to us how it was difficult to book inventory in and out, causing many people to just skip it altogether, leading to inaccuracies in the data. With spare parts, you need a lot of information to be accurate. So, the tool actually enabled the users to get the job done, but not in a way that ensured repeated success.
Another common problem we came across was finding the right part. If someone was looking for a specific spare part, in many digital tools, they would first need to “guess” which field to use for search. And when searching through descriptions to find where to find it was almost like a guessing game. You had to try to anticipate what the person had written down when they created the record in the tool.
One of the key points of user experience is the acceptance of a universal rule: If a process is not smooth, people will take shortcuts. Or to be more precise, the more effort you ask them to put in, the less they'll do.
For example, if they must enter a description, they'll add the minimum amount of information possible to move to the next step. If a tool doesn't specifically ask for a manufacturer's name (that’s actually quite common), they won't add it to the part’s record. This can cause problems later, for example when a technician is looking for that part, or when a procurement manager is trying to repurchase it.
Q: Why do you think this happens?
We noticed that spare parts are often an afterthought in different areas of the company. Even when selecting an ERP, companies focus on different activities, like managing their own supply chain, before looking at the ERP's capabilities in the area of spare parts management. This leads to very large companies managing massive amounts of spare parts in Excel spreadsheets.
And while it might be funny to think of large, well-known companies using Excel spreadsheets, people do prefer them for a reason.
Alternative software solutions are oftentimes too complicated. That's one reason causing some companies to simply ignore spare parts inventory planning altogether. Instead, they opt for a fixed re-ordering plan that never changes.
So, during times like the pandemic, when lead times increased by as much as 500%, we saw that some companies were still ordering the same amount of parts. When the pandemic ended and inflation began to shrink the market, they continued to order the same amount of inventory at the same time. This means that at any given time in the last five years, they were either under-ordering or over-ordering.
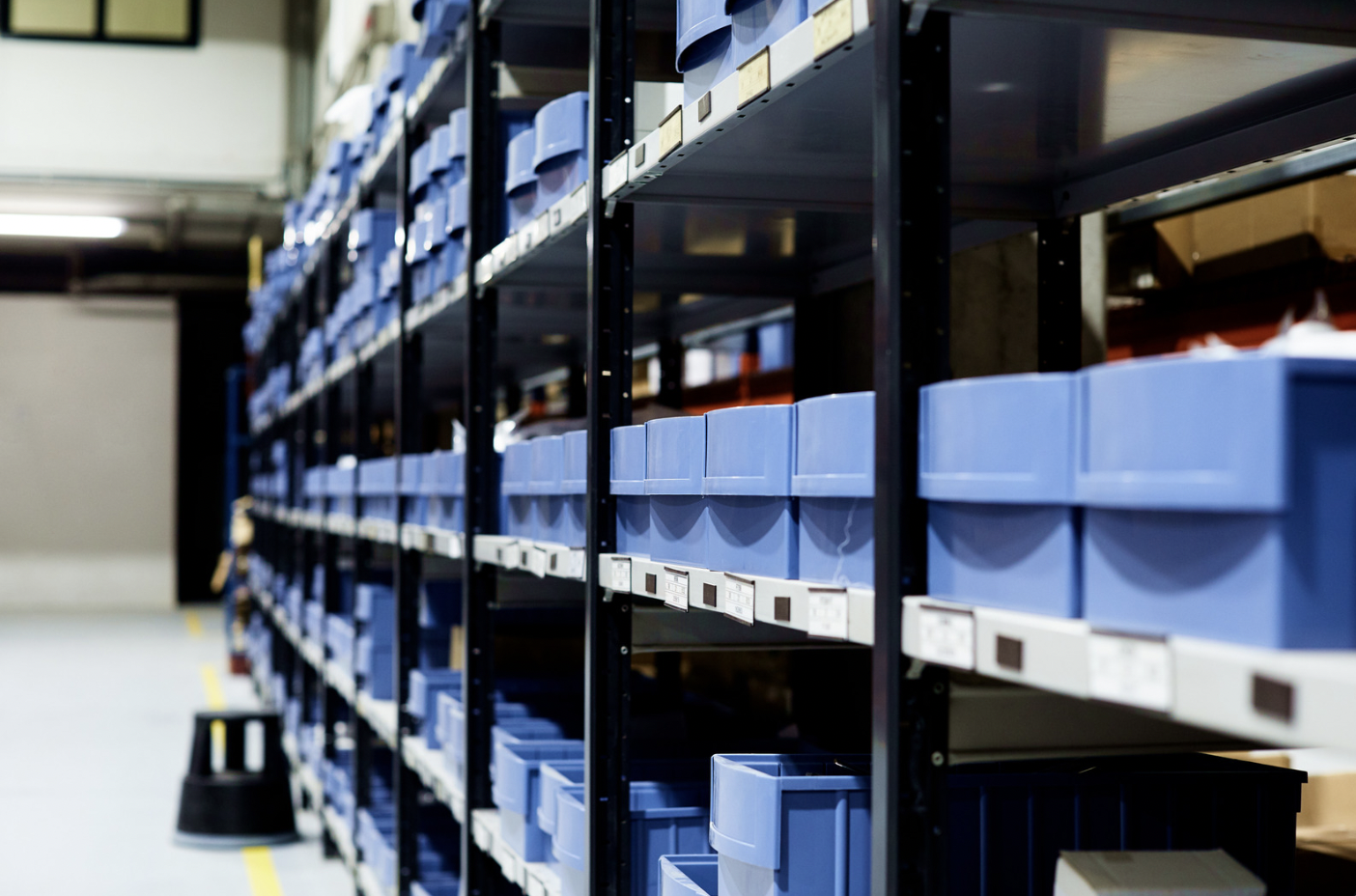
Evaluating user experience for spare parts management tools
Q: So, how should companies begin evaluating user experience when looking for new software tools?
This was the next question we had to ask ourselves as well. We started by thinking about a couple of key things that organizations are looking for when they want to evaluate a new tool. The first is the cost versus what the return on investment (ROI) will be. The second is to track both qualitative and quantitative metrics, such as how easy it is for someone to use the tool or how fast the process is with the tool compared to the traditional method. And, in more sophisticated cases like spare parts management, they generally look for some sort of requirements list where they start to compare features against each requirement.
Companies will almost always purchase a tool if it can prove that it solves the problem with a positive ROI. Few companies, at least at the time we'd started, considered user experience as a requirement or feature. Most companies don't have an objective way of evaluating a tool's user experience, and it would be difficult to develop one internally. They would need to create a structured way to do this, with each use case and potential user in mind.
Q: If you were to advise a company on how to measure user experience for a new tool then, where should they ideally start?
They would need to develop some kind of structured questionnaire to answer the question: "How convenient is this tool to actually use?"
I suggest starting with cataloging the main 5-10 tasks the tool would be used to on a recurring basis. Once these are defined, let as many potential users interact with the tool and grade each task on ease-of-use and time-to-completion. Aggregate the scores and try to come up with a unified score for each application’s user experience. Of course, leave room for qualitative input. Generally look for feedback like: “this tool made my work so much easier!”
Regardless of how this is done, having this kind of feedback can prevent companies from making poor choices about software solutions.
The turning point: When user experience becomes invisible
Q: You mention evaluating user experience for a new tool. What happens if a company already is using a tool? How can user experience be tested in this scenario?
Evaluating user experience for an existing application is harder than it seems. Users are already “used” to the way things are done. Some users are reluctant to change and will always say: “all’s good” even when things are not. That's why user experience issues surface after a new tool is implemented. Rarely do you get valuable feedback that leads to positive change after a tool has been used for long enough.
If you suspect there’s an issue with spare parts management in your organization, have a look at your processes. How many steps are involved in creating a new material or booking out a part? What information does the user need to have when going through these steps? If you haven’t done this so far, try “shadowing” a user. See where they get “stuck” or completely abandon a process.
Of course, you can also use a similar approach as described before, prepare a questionnaire and circulate it among your team. When preparing the questions and interpreting the results, you’ll need to account for the fact that users are more familiar with the tool.
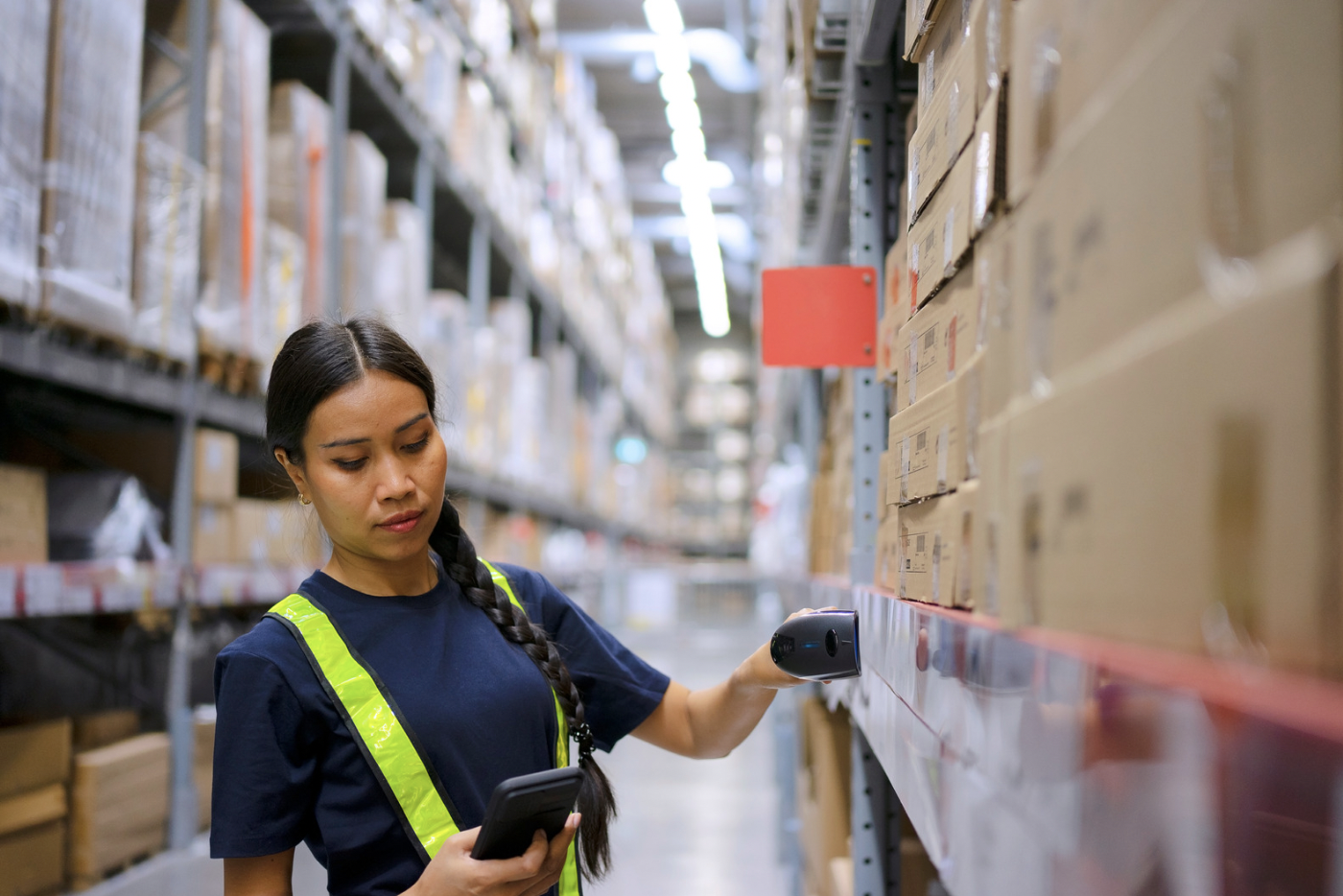
The alternative approach of process-based metrics testing
Q: That’s interesting, but it sounds like what you’re saying is that there is no way of testing user experience for tools that are already being used. Is that correct?
Not exactly. It might be much more challenging to test user experience once a tool is widely used, but it’s still possible.
At this stage, organizations have to approach user feedback a bit differently, with a shift to process-based metrics instead, or running tests to gather specific types of data to see if there might be a problem with the process or the tool that’s being used.
Generally, our recommendation is to start with either a process that you'd like to improve or a problem in a process that you'd like to solve, rather than a tool.
I've been using the example of booking inventory, so we can go back to that.
If you take a closer look at the booking process, you may find that you need a lot of controls, rules, and incentives to get the inventory done correctly. This is a good point to ask yourself: Does this process need a different tool?
Another good example is when people are searching for parts. You may find that because people have a hard time figuring out where the parts are, work orders take a lot longer than they should. This is also not the technician's fault. There's no way for someone to know where 10,000 parts are and how they're described. This could be another process that would benefit from a tool.
Sparrow’s approach to user experience
Q: Thank you for the overview. But, now that we have a good understanding of user experience in spare parts management in general, I'd love to ask you to go a bit more in detail about how Sparrow solves this problem.
I’ll have to take a few steps back, just to provide a bit of background. We didn’t initially build Sparrow to address poor user experience. It was something we discovered over time.
During the early development stages, we recognized that most of the problems in spare parts management had a user experience component to them. Whenever we created a new feature, we had a close look at existing workflows. Now, you have to remember that except for being data-nerds we’re also super-optimizers!
One of our main products is spare parts optimization (Sparrow.Plan). We try to make each process do exactly what it needs to do, no more and no less. An ideal user experience is where the tool disappears and people are able to focus entirely on the work in front of them.
We designed our tool in the simplest way possible and tested it with real users, taking into account their current skills, available time, investment in learning, and mental bandwidth. It worked so well that Sparrow is now used by thousands of spare parts professionals worldwide.
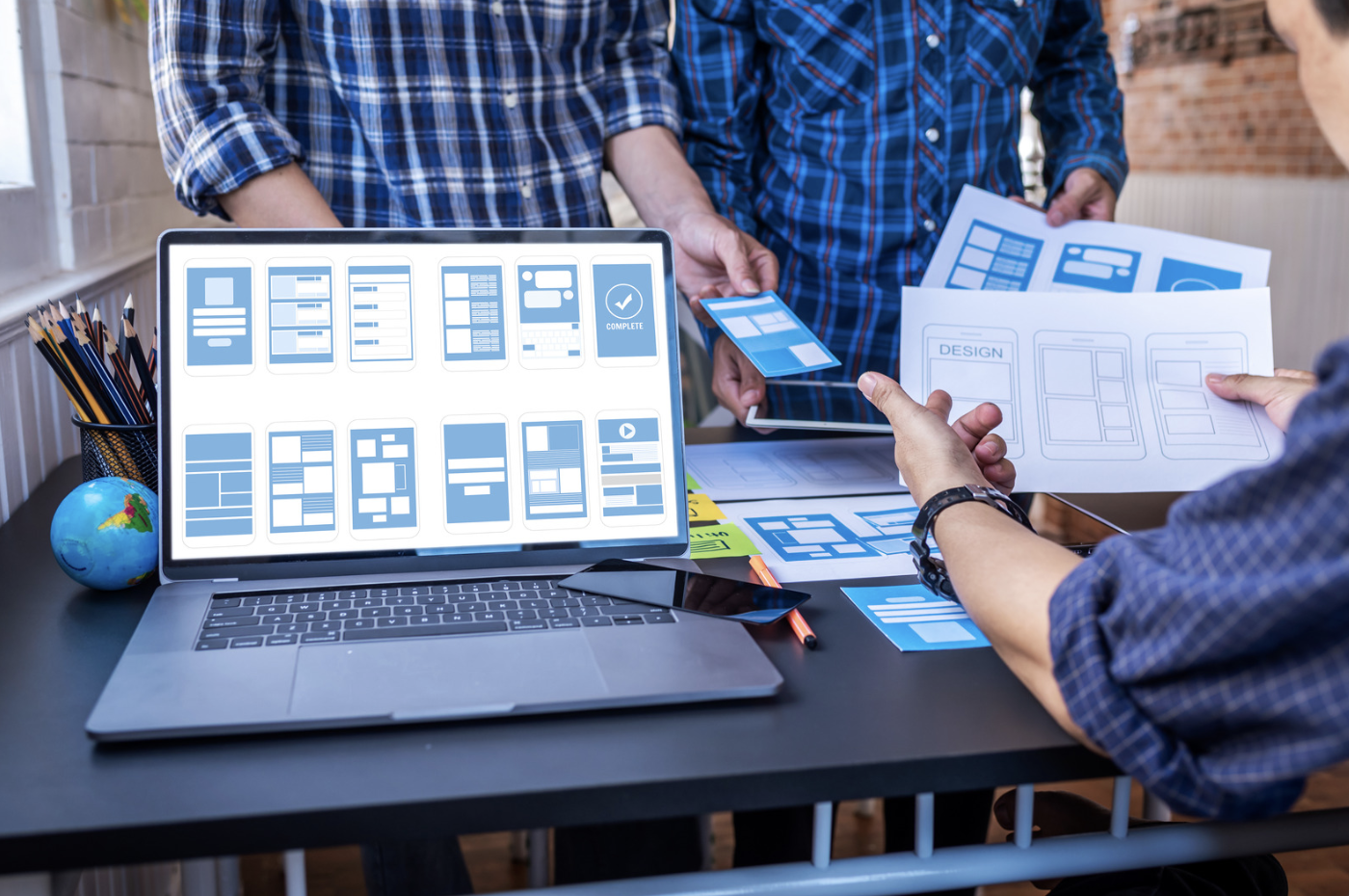
Q: What’s currently standing in the way of companies implementing similar tools on their own?
User experience may seem like an easy task, but it's actually quite difficult, which is often why companies look to external tools as a solution.
As I think I already mentioned, when we did our initial research with a few manufacturing companies, we found that several of them were managing very, very large inventories in Excel. While there's nothing wrong with Excel per se, it's a tool with severe limitations. There is no way to easily deduplicate parts. This would force anyone who wanted to create a version of Sparrow's data solution (minus the user experience) to develop their own alternative.
However, most manufacturing companies lack the resources to solve this problem. This is partly due to the fact that spare parts fall between the maintenance, procurement, and logistics teams. In addition, there's always pressure to reduce the cost of spare parts, and without a single team claiming ownership of the task, no one sees it as their responsibility.
It's also an incredibly complicated problem relative to its size in an organization. It's a mandatory process that needs to happen in a company and is financially quite significant, but it's also not part of the value chain. It's not part of anybody's core business, but it's incredibly complicated.
This signals to most managers and executives that trying to fix the problem might actually make things worse. Instead, they focus on the things they know they already do well — because, as we know, spare parts management has always been a problem. It's nothing new. Other challenges also have an easier return on investment due to simplicity.
It’s a vicious cycle, so having an external tool often solves this problem on multiple levels.
Q: Perfect! Thank you so much for the interview, and it was a pleasure getting to know more about Sparrow and your approach to user experience.
Curious to know what Sparrow looks like? Contact us to schedule a live demo, and we’ll be happy to show you!