A Deloitte study on the resilience of the spare parts market found that in many sectors of the machinery industry, it’s commonplace to see more than 50% or more of spare parts orders are marked as an emergency due to the severe consequences of not having certain parts available. Research also shows that investment in spare parts can represent 5% to 10% of a company's total investment base.
More troubling is that many companies already know that their spare parts operations are far from optimized — but don’t have the resources or tools to address these problems. In our experience, most struggle to identify the root causes or fear that changing their current processes could jeopardize their business.
With an interconnected supply chain involving multiple players and processes, identifying the changes needed can also be pretty challenging. But, the reality still remains the same: Many companies are not effectively managing their spare parts.
In this article, we’ll provide you with some of our experience in spare parts management to help you identify the most common issues within your spare parts operations so you can organize your inventory and save money in the future.
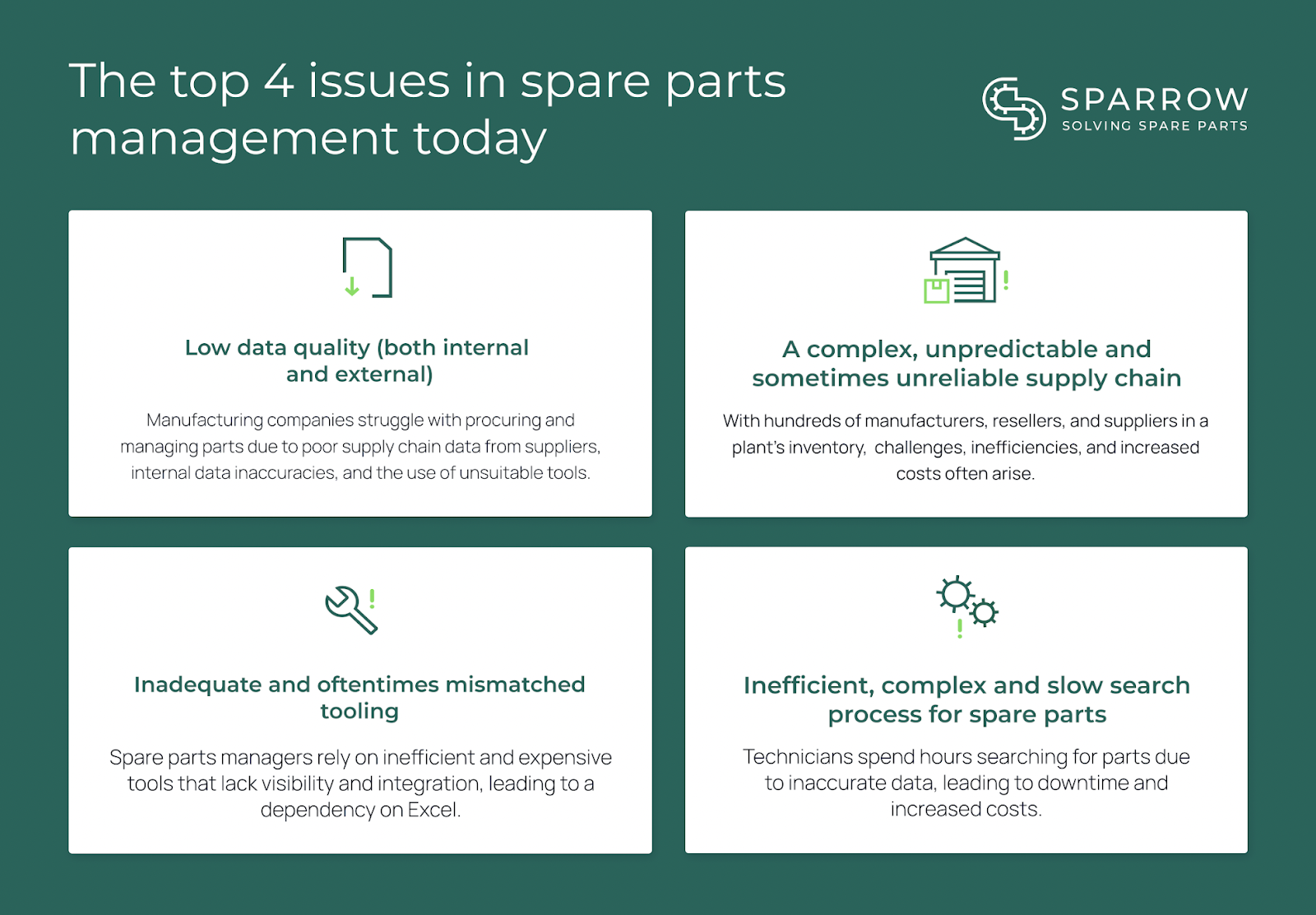
The top 4 issues facing spare parts management in 2024
Issue #1: Low data quality (both internal and external)
Most manufacturing companies report that they spend a significant amount of time and resources on parts procurement and management. Unfortunately, as you probably already know, many spare parts problems are simply beyond their control.
These problems often originate from parts suppliers who fail to provide sufficient supply chain data or visibility to improve operations. Without this data, companies simply cannot make effective procurement decisions. For example, take a company that typically purchases parts from a reseller. When an obsolescence notice is issued, it goes to the reseller and often isn't communicated to the company that ultimately purchased the part.
In addition to these external data challenges, companies also face internal data challenges.
Our experience shows that many companies still don't use enough automation to manage parts, resulting in cluttered spreadsheets that often gather dust and increase inaccuracies. Misclassification, incomplete part information, missing attributes, or different names for the same parts can also render a data set almost useless.
Many companies also still rely on semi-manual processes that require multiple separate files to be handled simultaneously (for example, each plant might have a different Excel sheet for their spare parts management). As a result, even when both external and internal data exists, it can be difficult to find and use effectively.
Moreover, a lack of digitization isn't always the problem. When material managers use different tools or platforms across different sites, it often becomes difficult to maintain data consistency across departments and locations. This problem is made worse when parts management responsibilities are spread across multiple departments.
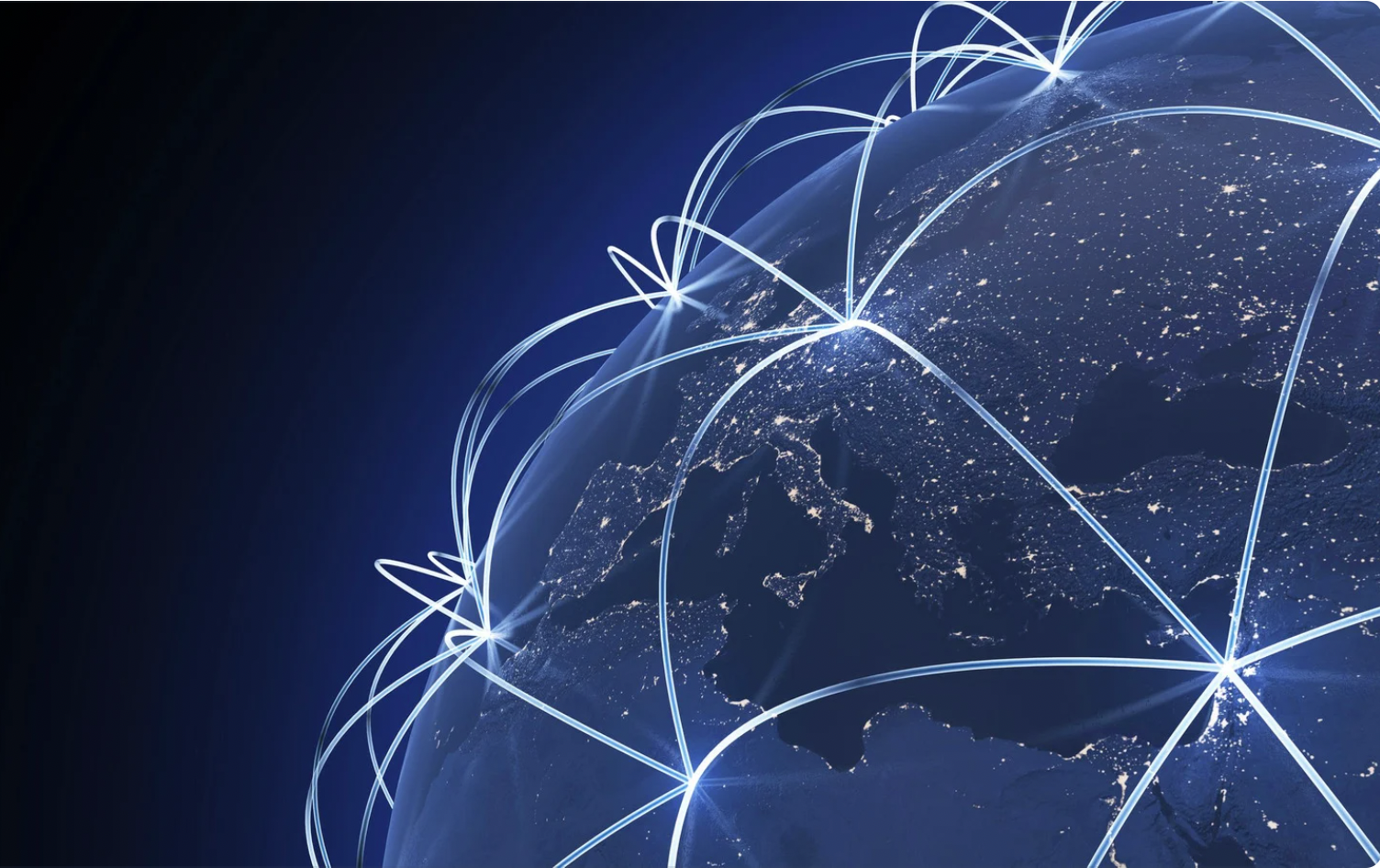
Issue #2: A complex, unpredictable, and sometimes unreliable
supply chain
Stockrooms at plants can have up to 1,500 manufacturers, resellers, and suppliers, which each have their own lead times and logistical challenges. Just the number of suppliers alone can complicate the entire spare parts procurement process, making it difficult to ensure that all necessary parts are available when needed. This complexity also often leads to inefficiencies and increased costs, as companies struggle to coordinate orders from multiple sources.
These lead times aren’t short, either. On top of this, they’re also often unreliable, too. More than 50% of orders encounter delays that exceed 30% of the expected time of delivery, which disrupts production schedules and can cause unplanned downtime. The level of unreliability is a significant challenge for manufacturers and companies that depend on precise timing to meet production deadlines.
When expected delivery times are not met, it can create a ripple effect throughout the entire production process, leading to missed deadlines and increased pressure on spare parts managers. For example, a 2022 survey found that 78% of manufacturers had experienced a shutdown or line stoppage due to a lack of spare parts
Managing spare parts involves more than just tracking inventory. It requires a strategic approach to ensure the right parts are available without overstocking or understocking. Companies need robust systems to monitor usage, predict needs, and quickly respond to demand changes, often using advanced software and data analytics for better supply chain visibility and decision-making.
Issue #3: Inadequate tooling
From inventory management to data management, tools used in the company are typically not geared for spare parts use cases.
The cost of spare parts for business operations often means looking for relevant tools to help with automation. What most material and warehouse managers find, however, is that most software solutions are incredibly expensive, difficult to use, and have pretty low levels of visibility — which is why they often fall back on various "master" Excel spreadsheets.
Inadequate tools can manifest itself in two different ways:
- The tool is missing key information, so it doesn’t have a clear overview of the stock levels in different warehouses or sites.
- Because of poor data quality, it’s practically impossible to use the tool when searching for parts. So, team members have to run around various sites looking for spare parts that might not exist.
What's more, because spare parts problems (and their spreadsheets) are so common, companies are often unaware that solutions exist outside of features in traditional ERP systems. And, when a solution does exist, many are unsure how to integrate it into their regular processes, including how the data from the master Excel sheet will be transferred to the new software accurately or if teams will accept the changes.
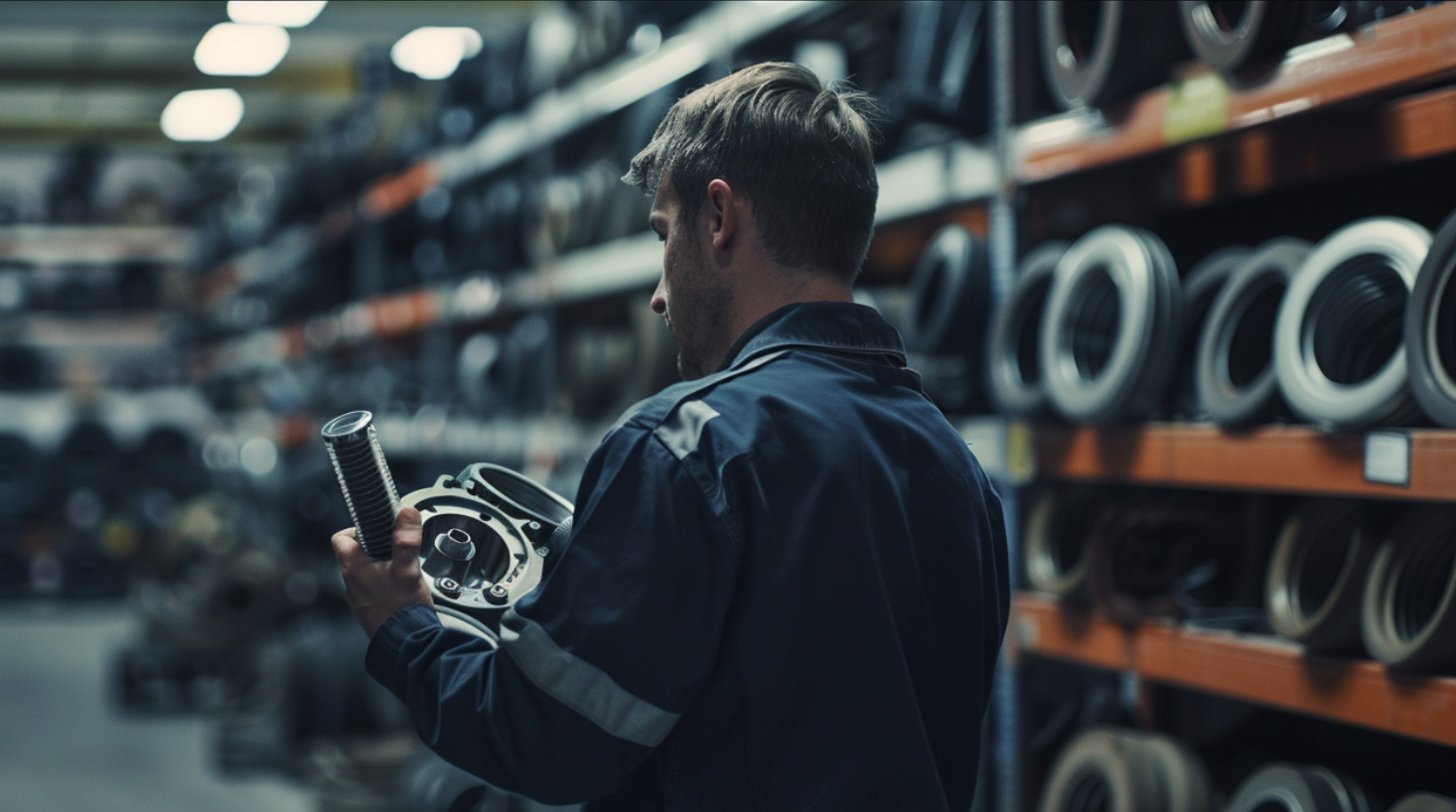
If spare parts managers want to become efficient and save resources, they should start digitizing their processes to source potential spare parts across their whole organization. To do this, businesses could pool their machine parts through a cross-site or cross-organizational system.
Digitizing spare parts processes helps combine data from multiple warehouses into a single system. Having a single tool that organizes the data when parts are added helps to standardize and clean this data across sites as well. When we developed Sparrow, we created a web-based application that incorporates external data on parts sources and intelligent data analytics to facilitate better planning, allowing companies to carefully review the status of the supply chain at any given time.
We’ve seen time and time again that when spare parts managers operate site-by-site, they often lack an integrated sourcing system, leading to missed opportunities with nearby spare parts. By sharing data through a single intelligent solution, managers can eliminate silos and make more efficient, cost-effective decisions.
Issue #4: Parts are extremely hard to find in warehouses
Searching for parts has never been easy. With disconnected and often inaccurate data, technicians often spend hours chasing parts that sometimes don't even exist.
Imagine a scenario where a machine breaks down and a key part is needed to repair it. The machine is critical to production, causing unplanned downtime at the plant. A technician is called in to fix the machine and sees that the part is supposed to be in stock at a nearby warehouse. After driving to the location and searching the designated shelf, the part is nowhere to be found.
After hours of searching nearby shelves, it was determined that the part was likely never there due to duplicate data entry. The technician reports back to the purchasing team, indicating that the part must be ordered immediately before production can resume.
Unfortunately, this scenario is all too common in service parts management. Technicians often fail to realize that the part may be available at another warehouse or plant, which would be significantly faster than sourcing new parts from manufacturers or resellers.
The problem is made worse when it comes to procurement. Depending on the part and its availability, procurement teams often struggle to find a suitable replacement. In many cases, parts are also obsolete or no longer available from original manufacturers or suppliers.
This not only delays the repair process but also increases costs, as procurement teams may need to source parts from secondary markets or consider custom manufacturing alternatives, which are often too slow (as downtime has already started) or unable to build the correct part.
Fixing spare parts management issues unlocks SMEs
As we’ve discovered, spare parts management can be very complicated if a company lacks the right approach and the right tools. Although there are still many gaps that exist between the latest research and how spare parts are managed on the ground, businesses shouldn’t be concerned.
Instead, we suggest acknowledging the issues and taking them as potential chances for improvement. In the end, a majority of companies are currently struggling to manage their spare parts, which means manufacturing companies have the opportunity to digitally innovate to gain a competitive advantage in the industry of tomorrow.
Indeed, a recent study by the University of Valladolid, in Spain, found that if stakeholders in the spare parts supply chain were to digitize their operations, (in terms of more effective logistic management), customers (in terms of response time), and the environment (in terms of reduced energy, emissions, raw materials, and waste) would benefit.
This means all four issues mentioned in this article can therefore be avoided using the right technology and data!
Did you know that’s actually the entire thinking behind Sparrow? We developed a software solution to solve all-things spare parts — including a digital supply chain for spare parts in the lime industry.