Meet Barry
Meet Barry: he’s an “Industry Connector” at AXOM (these days we don’t say spare parts manager anymore) working in a factory in the West of Germany. It’s 22nd November 2030, 9:06 am, and Barry’s taken a sip of his first coffee of the day. He walks from his kitchen to his open-plan home office area. “God I needed that”, he thinks, as he slurps away, surveying the virtual overview of the factory floor on the largest of his three monitor screens. He taps his wireless trackpad and scans the three screens he checks every morning, eyes squinted slightly. 49/50 of the plant’s machines are running smoothly: “don’t tell me number 033 is having issues again”, he thinks, mouth hovering before the next sip. No: it’s machine 018. This is unusual, “machine 018 is usually a good ‘un!”, he thinks.
He moves the mouse over to screen 2 and checks the status on the Fix’r desktop app: all fine there. He looks over the Fix’r operations record. Last night, the app had already identified the problem, a faulty part, and found some options: get the part delivered by midday for more than he’d usually be comfortable paying, or source a part free from another company plant a day’s driving away (“thank the lord for internal pooling”, Barry thinks to himself). Barry rubs his chin. No, not worth waiting, he thinks. It’s Christmas and all machines need to be running at high performance. “Fix’r, process Option 1”, he says towards the computer.
Meanwhile, Fix’r pops up with his daily “good morning!” overview. Highlighted in yellow, Fix’r warns that machine 42 is likely to need a new Sonic Compressor in approximately 25 days. “Well, what are the options Fix’r?”, Barry asks, perusing a digital twin of machine 42, on which Fix’r has marked out potential weaknesses. “There is one part located in an AXOM factory 500 kilometers away, with a delivery time of approximately 2-3 working days'', Fix’r cheerily (but, admittedly, somewhat robotically) chimes back. “Alright, do it Fixie”, Barry chirps, putting his coffee cup back a little too enthusiastically on a dog-eared cork coaster on his glass desk.
“Well, that’s the first bit of my day done”, Barry reflects, as he logs into AXOM’s staff wellbeing portal and selects his usual 9:45 am “Yin-Yang” online yoga class. “Fix’r, hold the ship down, I’ll be back in 60 minutes!”, he yells, rolling out his yoga mat...
The Future of Spare Parts: Coming Your Way Soon
Barry’s morning routine may feel like it’s lightyears away, but spare parts management is a hotbed of underground innovation right now. His story offers us only a few insights into how spare parts management could look in the next 10-20 years. New business and operational models are emerging as technological developments and financial pressure shake up how spare parts management is done in the day-to-day.
We’ll sort the hype from true innovation and take a deep dive into what the future of spare parts could look like for your business.
The Future of Spare Parts: Coming Your Way Soon
The Spare Parts Innovations You Need to Know About
1) Spare Parts as a Service
The subscription model has taken over nearly every area of our lives - from music (Spotify) to fitness (Class Pass) to work (even Microsoft is now doing it!). The spare parts business is no exception. There are two key subscription options for spare parts.
Spare Parts Access as a Service
Here, you pay a subscription fee to have access to spare parts quickly. You still need someone in-house overseeing spare parts, but you no longer need to stock any. Instead, your subscription fee pays a company who owns the parts, or who may themselves contract someone else who does. The aim of this is to stop you from having to invest in spare parts (CAPEX), while also giving you access to a service that probably guarantees a maximum delivery time for critical parts that’s lower than what you’re dealing with now. Moreover, the parts you receive are always the right, best and newest parts. This beats old or even obsolete parts that have been sat on the factory shelves for years.
Maintenance as a service
This model is more or less uptime as a service. What this means is that the company offering the subscription takes care of the whole lifecycle of your machine. So they more or less take over spare parts management for you, as part of a bigger package effectively looking after the overall maintenance of the machine. This service is increasingly offered by the manufacturers of machines, as an extension of the warranty (a bit like Apple Care), but also by other companies.
It’s important to note that this idea is not exactly new: manufacturers and other companies have been doing this for a while now. What’s new is that the machine operators have stopped selling (just) the machine, and are instead selling the output/availability. So, instead of selling a bottling line, the machine builder might now sell uptime hours or even a certain quantity of bottles.
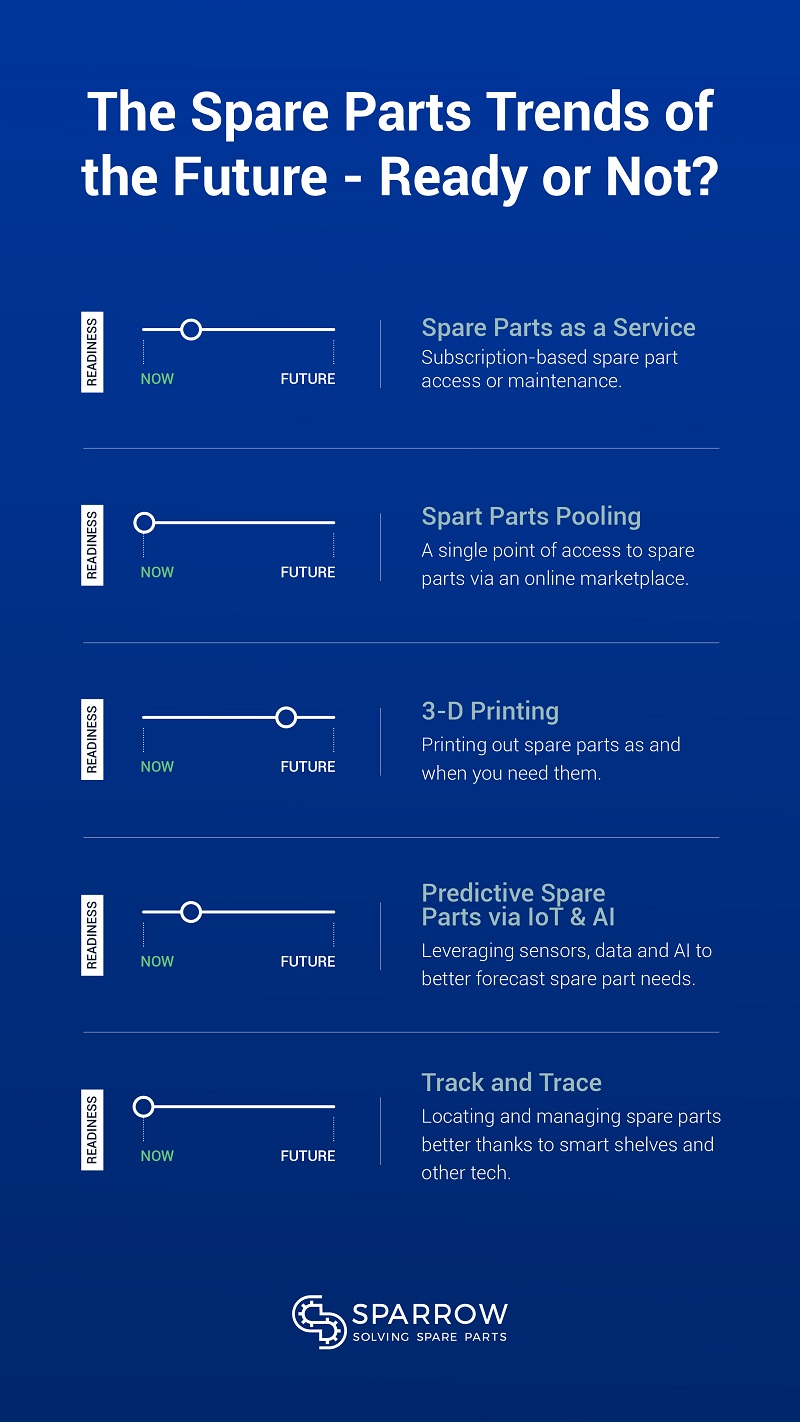
2) Pooling
Spare parts pooling means creating a single access point for all spare parts. This can be done, for instance, through an online spare parts ‘marketplace’ system. There are two different levels of pooling. The first is internal pooling, where all the spare parts within your company, across all your sites, are accessible in one place (probably an online platform). This way, anyone who needs a spare part can access one internally at any given moment.
The second is external pooling, where you enter a pool with external parties outside your company, for example, other similar companies, suppliers of spare parts, machine manufacturers, and so on, either only as a buyer of spare parts or a seller too. The IATP - International Airlines Technical Pool - a pool of over 100 airlines sharing aircraft recovery kits, aircraft parts and tooling, ground handling equipment, and manpower/facilities - is probably the best global example of an external pool. To find out more about pooling, take a look at our last article.
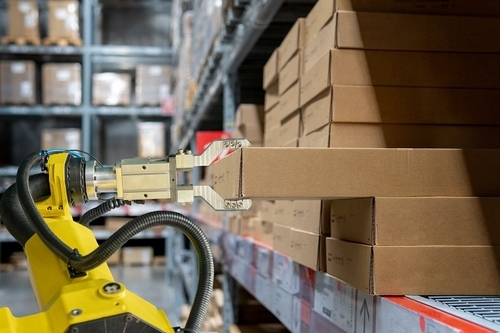
3) 3-D Printing
3-D printing is what it sounds like: printing out spare parts as and when you need them. Instead of stocking spare parts in real-life, instead, you stock them in a “virtual inventory”, and simply select to print them when you need them. 3-D printing sounds amazing - it offers decreased storage costs and the possibility to print any part at any moment, which is particularly appealing for low-volume production.
However, it’s not a very viable option right now for many industries and doesn’t look like it will be anytime soon. Although, of course, there are some industries (mostly aerospace) where this is already the reality, for most others, it’s very far from being the best option. First of all, 3-D printers are extremely costly and take a long time to print products. It’s not like printing off a two-second flyer: physical objects can take anywhere from 1-5 days to print. Secondly, 3-D printers can’t yet print in all materials. Yes, metal-printing is possible, but not for all types of metal, and this may pose big problems for producing certain spare parts. Thirdly, some spare parts won’t necessarily be available for free-printing - their design may be owned by the company that manufactured the machine and limited to use only by other companies who have a license. Nevertheless, this is still one to watch as it does promise some good things.
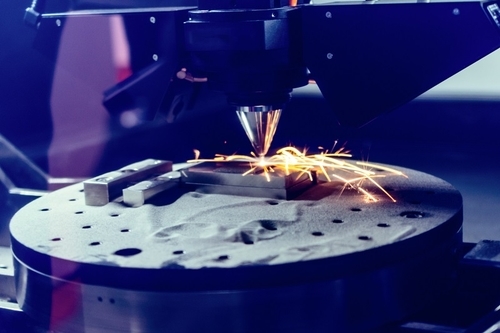
4) Predictive Spare Parts via IoT and AI
The Internet of Things (IoT) and Artificial Intelligence (AI) are often upheld as a panacea to all the world’s problems. Certainly, we should be skeptical about their application in some areas, but when it comes to spare parts, they could be extremely useful.
IoT in spare parts works by placing sensors in machines to monitor their performance and flag when a part needs replacing. These sensors send data to gateways wirelessly, which then feed it through to software, where it can be visualized and/or analyzed for the end-user (here, a spare parts manager). AI comes into play here in the analysis of the data; any software employing data analytics to model what could be happening with your machines is using artificial intelligence of some kind. There’s also increasing talk of “digital twins” in the manufacturing world: virtual replicas of the factory floor, which can “run” as a simulation (usually based on previously collected sensor data) and similarly model when machine maintenance needs to be done (or spare parts bought).
The basic fact is: if you have enough sensors in enough machines, you have a lot more data with which to model and predict (via AI) when you might need spare parts. And this only grows with time - the longer you have sensors in a machine reporting on its performance and flagging when a part breaks, and the more machines this is happening in, the more accurate your predictive models will be. This allows operators to better plan - they can know that a specific part in a specific machine will probably break in 3 weeks so that if they order it within 1 week, they’ll be covered and avoid any downtime. you’re good. This means they don’t have to wait for a part to fail: they can replace it in advance.
This is likely to be quite standard in the future. There are, however, some barriers to this method at the moment. The largest being that many machines don't have sensors yet, companies don't have the tools and skills to run these analyses, and, therefore, current predictions made via IoT and AI are generally not as precise as we would need them to be (we really could do with knowing if a part will break imminently in the next 2 hours or the next 6 months). This means that some serious investment in the right equipment is needed over the next few years to make predictive maintenance properly viable and effective.
5) Track and Trace - Locating and Managing Spare Parts Better
Finding and locating spare parts is a lot harder than you might think when you have hundreds or thousands of them spread across different sites. Often, companies simply don’t know how many of a certain spare part they have (or if they have it all), which can be extremely costly and wasteful. With RFID (Radio Frequency Identification) and “smart shelves”, this is solved. RFID tags contain tiny radio transponders, allowing electromagnetic fields to be used to automatically identify and track them. When you attach these tags to objects, the latter can thus be located and tracked. Using a “smart shelf” system where all spare parts are tagged thus enables you to know exactly how many parts you have on your shelf. This is not just a helpful extra: it’s desperately needed. Stockroom workers may be working in an environment with 10s of 1000s parts that they need to identify very quickly. If data are missing - or they just don’t know how to find the part in question - the whole factory’s operations can be held up. RFID is one way to solve a difficult problem with a simple solution.
Hype or True Innovation for Spare Parts? Our Top Picks
Our top hype: 3-D Printing
Why?
The hype is real when it comes to 3-D printing: it seems like an amazing golden bullet solution, but the technology is just not up to scratch yet and there are lots of unforeseen hiccups that prevent it from being the dream spare parts cure we’re all looking for.
Our top true innovation: Pooling
Why?
The science is on the side of pooling and it's a simple but highly effective strategy to implement. On a basic level, when pooling, you become tremendously efficient - and this efficiency leads to massive cost-savings. For example, a 2009 case study by Kranenburg and van Houtum at ASML, an OEM in the semiconductor industry, showed that pooling could save on spare parts management by up to 50%. A 2014 article by Karsten and Basten also similarly suggested that annual savings of 44% could be obtained via pooling.
New tech will make the spare parts management industry smarter and better
In the end, these are only 5 possible innovations in the spare parts industry. There are plenty more not discussed in this article that already exist - or will emerge in the coming years. In reality, spare parts management in the future will probably combine many or all of these strategies and technologies to achieve the optimal operational model. For example, you might pay for a subscription service with a company that offers an intelligent pool that uses AI to find you a spare part as quickly as possible across multiple stock rooms, all using RFID tagging. It’s not a question of finding the best spare parts method, but rather figuring out which operational innovations (in terms of process, or technology) can best optimize your particular company’s business model. This is the only way to future proof your business, while also helping it to grow in the here and now.